The NEMO project “Near-zero-waste recycling of low-grade sulphidic mining waste for critical-metal, mineral and construction raw-material production in a circular economy’” is a EU H2020 Innovation Action project (IA, call SC5-14b). Using a “4 PILOTS – 2 case-studies” concept, NEMO develops, demonstrates and exploits new ways to valorise sulphidic mining waste.
Public NEMO abstract
With an estimated volume of 600 Mtonne/yr and a historic stockpile of 28,000 Mtonne, sulphidic mining waste from the production of Cu, Pb, Zn and Ni, represents the largest volume of extractive waste in Europe. When poorly managed, these “tailings” may cause major environmental problems such as acid mine drainage. In 2016 EIP Raw Materials launched a “call to arms” to transform the “extractive-waste problem” into a “resource-recovery opportunity”, as “tailings” still contain valuable & critical metals. Using a “4 PILOTS – 3 case-studies” concept, NEMO develops, demonstrates and exploits, therefore, new ways to valorise sulphidic mining waste. The 3 cases are the Sotkamo Ni-Co-Zn-Cu mine in Finland, the Luikonlahti processing facility in Finland and the Tara mine in Ireland; the 4 PILOTS are located at key points in the near-zero-waste flowsheet, encompassing the recovery of valuable & critical metals, the safe concentration of hazardous elements, the removal of sulphur as sulphate salts, while using the residual mineral fraction in cement, concrete and construction products. NEMO has established an interdisciplinary consortium, including 8 industrial partners (2 mining, 4 engineering, 1 machine manufacturing & 1 construction material company), 4 research institutes, 2 universities and 1 civil society group. NEMO’s near-zero-waste technology will provide the EU with both direct and long-term, indirect advantages. The former range from new resources (e.g. base metals: Cu, Zn, Ni, Au; critical metals: Co, Sc, Nd, Y, Sb; SCM and aggregates etc.), CO2 savings from metal recovery and the replacement of Ordinary Portland Cement), new job creation, new revenues from the multiplication of the former benefits, while eradicating acid-mine drainage and other environmental issues, and ensuring an enhanced dialogue (framework) between industry and civil society, to obtain and maintain the License to Operate mines in EU.
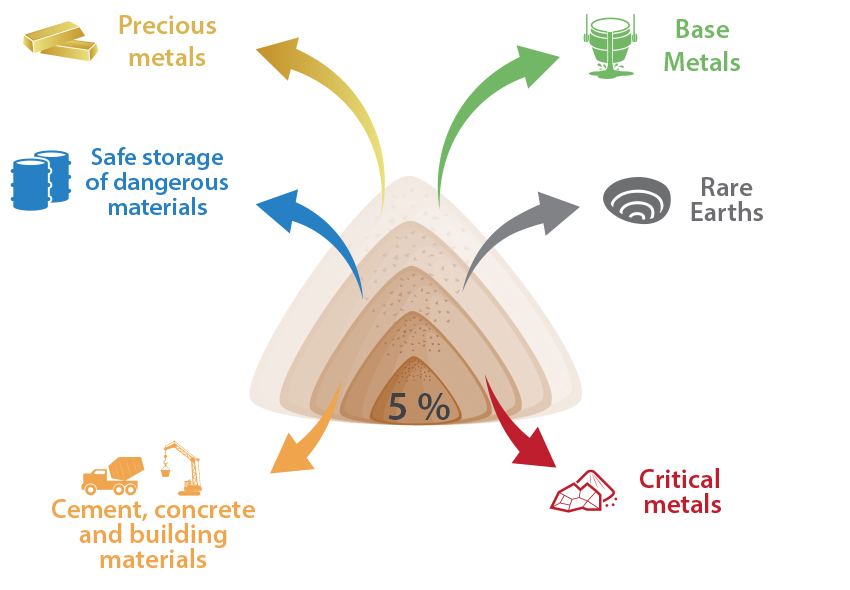
Figure: The NEMO concept. Sulphidic mining residues are at present times typically deposited in tailing storage facilities. NEMO aims at further treatment of these residues to recover valuable metals and minerals, while concentrating hazardous elements and using the residual matrix in cement and construction materials.
The structure of the NEMO project is indicated in the Figure below. The two NEMO case studies are:
The Sotkamo Ni-Co-Zn-Cu mine, Finland. Residues of the primary heap-leaching operations of the mine are subjected to pond bioleaching and, alternatively, to secondary heap bioleaching. The enhanced bioleaching aims at improving the recovery of Cu, Co, Zn and Ni. Recovery of additional metals such as REE, Mn, Mg, Al, Fe and Sc is also aimed for. The residual mineral matrix after enhanced bioleaching is used for production of cement, aggregates and construction materials.
The Luikonlahti Cu-Zn-Ni-Co-Au-ore processing facility of the Kylylahti mine, Finland. High-sulphur tailings from the Luikonlahti processing facility are treated further using a tank bio-leaching processes aiming for the recovery of Co, Ni, Cu and Zn. Residual precipitates and the mineral fraction are stabilized or converted to be re-entered in the plants process flowsheet.
The Tara Zn-Pb mine, Ireland. Tailing slimes are used for the production of cement & concrete, i.e. a novel composite cement by flash-calcination of tailings, artificial aggregates by granulation of tailings, demonstration of ready-mix concrete production and application and pre-cast concrete element production at an industrial scale.
NEMO composes 4 core science & technology work packages in which 4 pilots are developed to demonstrate different aspects of the conversion of sulfidic residues to metals, minerals, cement and building products.
WP1: Innovative bioleaching. Demonstrates bioleaching in ponds (pilot 1a) and heaps (pilot 1b) using the leaching residues of the primary heap leaching of the Sotkamo mine.
WP2: Tank bioleaching. Demonstrates bioleaching in tanks (pilot 2a) on high-S tailings from the Luikonlahti processing facility and the subsequent recovery of Co, Ni, Cu and Zn (pilot 2b).
WP3: Metal and mineral recovery. Demonstrates the recovery of additional metals (Cu, Zn, Co, Ni, REE, Mn, Mg, Fe, Al) from pilot 1 and from PLS from the Sotkamo mine (pilot 3).
WP4: Cleaned mineral residue upcycling. Demonstrates the production of cement, aggregates and construction elements from the residues after bioleaching, from the 2 NEMO case studies and from other mines in the E.U.
The 4 core science & technology work packages are supported by 5 work packages: WP5 aims at the integration of the 4 pilots into a near-zero waste pilot for processing of sulphidic mining residues; WP6 performs a sustainability analysis of the two case studies using life-cycle analysis, life-cost analysis and social life cycle assessment; WP7 supports clustering activities with related projects; WP8 studies the NEMO stakeholder engagement and supports in the communication, dissemination and exploitation of NEMO results; WP8 provides the management support of the project.